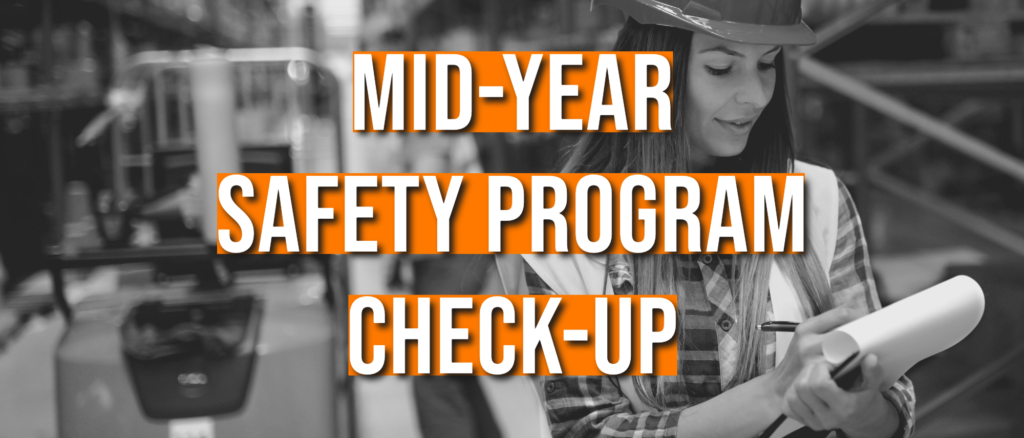
Helping companies reassess their safety strategies halfway through the year with a focus on compliance, PPE inventory, and training refreshers.
Mid-Year Safety Program Check-Up: What to Review and Update Now
As we reach the halfway point of the year, it’s a great time to pause and take a closer look at your workplace safety program. Even if your safety efforts have been running smoothly, a mid-year check-up can help you stay on track, avoid compliance issues, and ensure your team is well-protected for the rest of the year.
Start with a Compliance Review
First, review your current safety policies and procedures. Are they still in line with the latest OSHA regulations or industry standards? Safety rules are sometimes updated, and what was acceptable at the beginning of the year may need changes now. If any new regulations have been introduced, your safety documents should reflect them.
In addition, check that your records are complete and accurate. Training logs, inspection reports, and incident documentation should all be organized and up to date. If anything is missing or unclear, take time to fix it before the second half of the year brings more challenges.
✅ Compliance Review Checklist
View/Print/Download Printable PDF
- Safety Policies and Procedures
- Are your safety policies up to date with current OSHA and local regulations?
- Have there been any regulatory changes since the beginning of the year?
- Are your written procedures clear, accessible, and communicated to staff?
- Training Records
- Are all employee training records complete and current?
- Have new hires completed required onboarding safety training?
- Are there any employees due for refresher training or certifications?
- Incident Documentation
- Have all incidents, near-misses, and corrective actions been logged properly?
- Are follow-up investigations completed and documented?
- Are trends or recurring issues being tracked and addressed?
- Equipment and Facility Inspections
- Are inspection logs up to date for equipment, PPE, and facility areas?
- Have all required inspections (e.g., fire extinguishers, emergency showers) been completed?
- Are repairs and maintenance issues being documented and resolved quickly?
- Emergency Preparedness
- Are emergency action plans current and posted where needed?
- Have evacuation drills been conducted and logged?
- Are emergency contact lists and SDS sheets current and accessible?
- Signage and Communication
- Are safety signs, labels, and hazard warnings in good condition and visible?
- Is your safety communication plan (e.g., toolbox talks, alerts) being followed?
- Are employees aware of how to report hazards or concerns?
- Regulatory Reporting
- Have all required reports (OSHA 300 logs, environmental permits) been filed?
- Are records being kept according to legal retention requirements?
Check Your PPE Inventory
Next, turn your attention to personal protective equipment (PPE). Over time, equipment can wear out, become outdated, or go missing. Walk through your facility and evaluate what’s on hand. Are there enough gloves, safety glasses, respirators, and hearing protection for all employees? Is the gear still in good condition?
If you notice any shortages or damaged equipment, it should be replaced immediately. It’s also helpful to ask your team for feedback on what’s working well and what could be improved. After all, they are the ones using the equipment every day.
🧤 Essential PPE for Manufacturing Facilities
Head & Face Protection
- Hard hats (various types, including vented and non-vented)
- Face shields (full and partial)
- Safety goggles (chemical splash and impact-resistant)
- Safety glasses (with side shields or wraparound styles)
- Welding helmets (if applicable)
Hearing Protection
- Disposable foam earplugs
- Reusable earplugs
- Earmuffs (standard and electronic)
Respiratory Protection
- N95 disposable respirators
- Half-mask respirators with cartridges/filters
- Full-face respirators
- PAPR (Powered Air-Purifying Respirators)
- SCBA units (for confined space or hazardous materials)
Hand Protection
- General-purpose work gloves (cut-resistant, nitrile, leather, etc.)
- Chemical-resistant gloves (neoprene, PVC, etc.)
- Heat-resistant gloves (for hot work or welding)
- Anti-vibration gloves (for heavy equipment use)
- Electrical insulating gloves (if working near energized systems)
Body Protection
- High-visibility vests or shirts (ANSI-compliant)
- Flame-resistant clothing (if required by process or materials)
- Lab coats or smocks (chemical handling)
- Welding jackets or aprons
- Chemical-resistant suits or aprons
Foot Protection
- Steel-toe or composite-toe safety boots
- Slip-resistant soles
- Electrical hazard-rated boots
- Metatarsal guards (if heavy objects are handled frequently)
- Shoe covers (for cleanroom or contamination-sensitive areas)
Fall Protection (if working at height)
- Full-body harnesses
- Shock-absorbing lanyards
- Self-retracting lifelines
- Anchor points and connectors
Eye Wash & Emergency Equipment
- Portable eye wash bottles
- Plumbed eye wash stations
- Emergency safety showers
Additional Specialty PPE
- Arc flash suits (if working on or near live electrical systems)
- Disposable coveralls (for dust, paint, or light chemical exposure)
- Cooling vests or hydration gear (for high-heat environments)
- Knee pads or back support belts (for ergonomic support)
Refresh Training and Communication
Even the best safety plans don’t work without proper training. Now is a smart time to offer refresher courses or toolbox talks. These short, focused sessions remind employees of key safety practices and keep safety top of mind.
You should also look at how safety information is being shared. Are your team members receiving regular updates? Are safety meetings happening often enough? If communication has slowed, find ways to re-engage staff and encourage participation.
Use This Time to Plan Ahead
Lastly, use this mid-year check-in to plan for the rest of the year. Set new safety goals, schedule future audits, or prepare for seasonal hazards like heat stress in the summer or ice in the winter. Small steps now can prevent bigger problems later.
Final Thoughts
Staying on top of workplace safety takes effort all year long. However, taking the time in July to reassess your program helps keep your people safe, your facility compliant, and your operations running smoothly. A safer second half of the year starts with a strong mid-year check-up.
Checklists
View/Print/Download PDF Versions Below: